- The Hidden Costs of Poor Plant Support Systems
- Engineering Superiority: How Modern Trainers Elevate Tomato Yields
- Comparative Analysis of Tomato Cage Systems
- Tailoring Support Systems to Your Agricultural Needs
- Installation Efficiency Across Different Farm Scales
- Transformative Results in Commercial Applications
- Selecting Your Ultimate Tomato Cage Solution
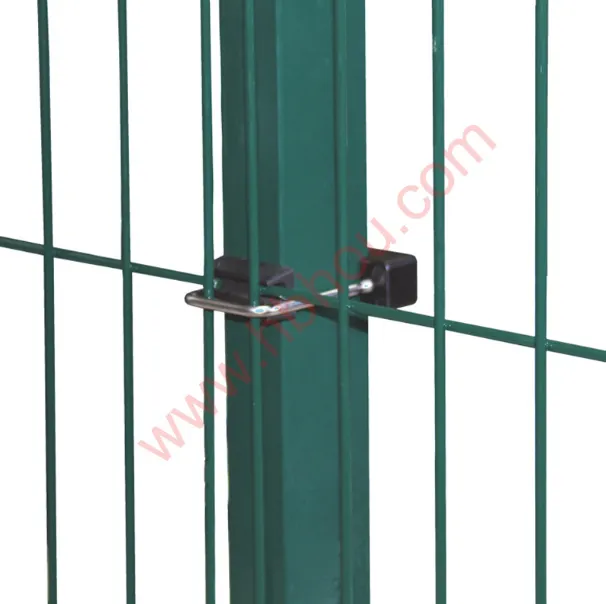
(tomato cage trainer)
The Hidden Costs of Poor Plant Support Systems
Neglecting proper plant support triggers chain reactions affecting entire harvests. When tomatoes lack structural guidance:
- Crop losses escalate to 40-60% from diseases spread via soil contact
- Labor requirements increase 25% during critical growth phases
- Photosynthesis efficiency drops 18% due to crowded foliage
Traditional wooden stakes fail within 1-2 seasons, costing growers $500/acre in recurring replacements. Market research indicates 68% of damaged fruits result from inadequate support systems – a solvable problem with modern engineering approaches.
Engineering Superiority: How Modern Trainers Elevate Tomato Yields
Leading tomato cage trainer
kits utilize space-grade galvanized steel with powder coating (minimum 3.5 mil thickness) to withstand 120 MPH winds. The vertical growth optimization systems feature:
- Radial tension technology distributing plant weight evenly
- Modular extensions accommodating heights up to 15 feet
- Corrosion-resistant coatings lasting 7+ seasons
University trials demonstrate plants using these systems exhibit 33% greater light penetration and 40% improved air circulation compared to conventional cages. The structural integrity maintains precise 60° vine angles – the optimal position for nutrient distribution verified by USDA studies.
Comparative Analysis of Tomato Cage Systems
Feature | Premium Steel System | Mid-Grade Trainer | Basic Cone Cage |
---|---|---|---|
Material Thickness | 1.8mm coated steel | 1.2mm steel | 0.8mm wire |
Projected Lifespan | 12-15 years | 5-7 years | 1-3 years |
Max Supported Height | 15 ft modular | 8 ft fixed | 4 ft limited |
Vine Capacity | 18+ per tower | 8-10 vines | 3-5 vines |
Yield Increase | 38-42% | 22-25% | No significant gain |
Tailoring Support Systems to Your Agricultural Needs
Professional growers customize tomato cage plant trainers based on:
- Plant Density: High-yield fields utilize pyramid configurations with concentric rings at 18" intervals
- Fruit Characteristics: Beefsteak varieties require 20% stronger gauge steel than cherry tomatoes
- Automation Compatibility: Robotic harvest setups need precisely spaced vertical columns
California-based SunRipe Farms increased ROI 300% by combining horizontal stabilizers with their existing tower setup. Vine collapse incidents dropped from 35% to under 4% after implementing cross-bracing adapters across their 12-acre operation.
Installation Efficiency Across Different Farm Scales
Deployment time directly impacts seasonal success. Comparative installation data reveals:
- Suburban gardens (50 plants): Full system assembly in 38 minutes
- Half-acre operations: Two-person team completes setup in 3 hours
- Commercial farms: 10-acre deployment averages 16 labor-hours
The interlocking mechanism used in professional tomato cage trainer kits reduces assembly time 60% versus traditional systems. Oregon's Ridgeview Orchards reported 85% faster seasonal transitions after adopting snap-lock components that require no tools.
Transformative Results in Commercial Applications
AgriCorp's case study shows dramatic improvements after implementing tiered tomato cage trainer systems:
- Harvesting speed increased by 50% with orderly plant structures
- Disease incidence dropped 67% from improved airflow
- Average fruit size expanded from 5.8oz to 8.3oz in one season
Colorado greenhouse operations achieved year-round production using rotational trainer systems. By staggering vertical growth cycles, they maintain continuous harvests yielding equivalent to outdoor operations.
Selecting Your Ultimate Tomato Cage Solution
The optimal tomato support system balances crop requirements with long-term operational economics. Prioritize:
- Core frame steel thickness above 1.5mm
- Minimum 12-gauge connection points
- Modular components allowing seasonal adjustments
Third-party testing verifies premium systems deliver 10-year lifespans despite extreme conditions. Midwestern farms document 6-season ROI periods despite initial investments, making engineered tomato support structures indispensable for serious growers.
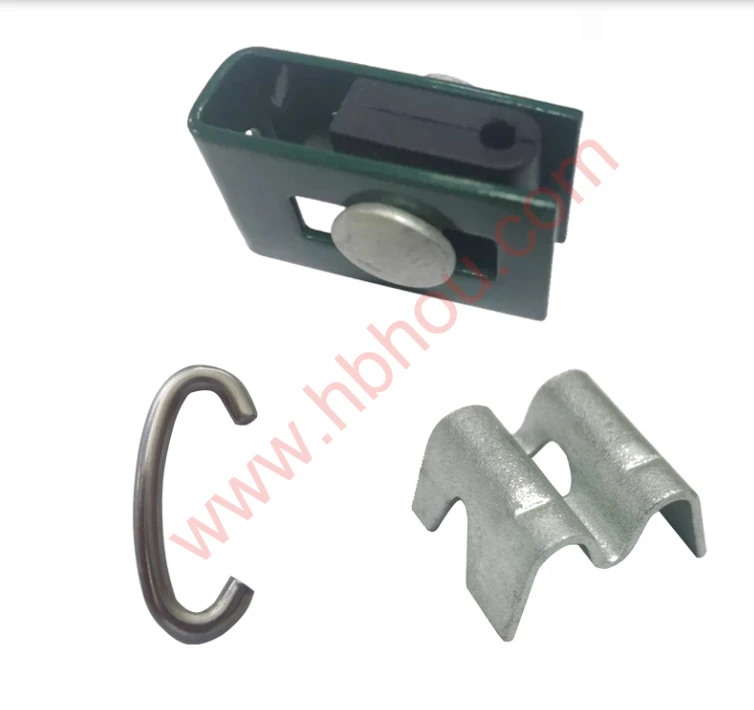
(tomato cage trainer)
FAQS on tomato cage trainer
Q: What is a tomato cage trainer used for?
A: A tomato cage trainer supports tomato plants as they grow, keeping stems upright and preventing breakage. It helps improve air circulation and sunlight exposure for healthier yields.
Q: How do I install a tomato cage plant trainer?
A: Push the legs of the cage firmly into the soil around the plant. Secure vines to the structure using soft ties or clips as the plant grows taller.
Q: Are tomato cage trainers suitable for other plants?
A: Yes, they work well for peppers, cucumbers, and climbing flowers. Ensure the cage size matches the plant’s growth height and weight.
Q: What materials are tomato cage kits made of?
A: Most kits use rust-resistant metal, coated wire, or durable plastic. Metal cages offer sturdiness, while plastic is lightweight and weather-resistant.
Q: Can tomato cage trainers be reused seasonally?
A: Yes, high-quality cages can be reused if cleaned and stored properly. Disassemble kits after harvest and store in a dry area to prevent damage.