- Core technical specifications and engineering advantages of gabion systems
- Comparative analysis of leading manufacturers using performance metrics
- Advanced project customization framework and design options
- Real-world implementation scenarios with structural performance data
- Geotechnical site preparation requirements and best practices
- Maintenance protocols and long-term structural behavior
- Cost-benefit evaluation across infrastructure applications
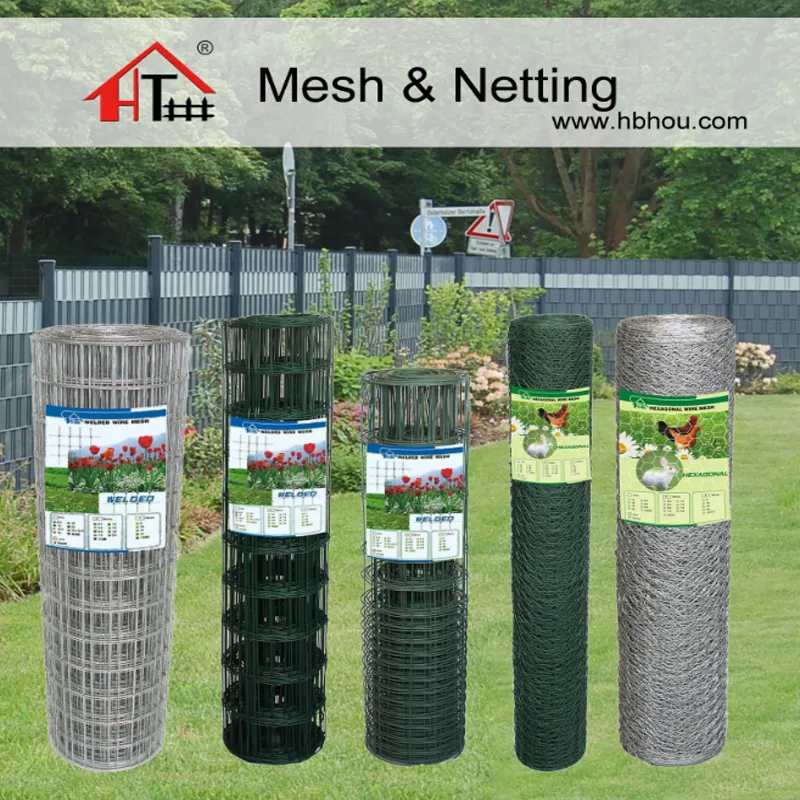
(gabion 400)
Gabion 400: Technical Specifications and Material Advantages
Gabion 400 systems utilize triple-twisted hexagonal mesh constructed from 4mm diameter wire coated with Galfan alloy (95% zinc, 5% aluminum-mischmetal), providing 2.5× enhanced corrosion resistance compared to standard galvanization. Rock fill requirements specify 90-250mm diameter quarried stone with minimum 24kN/m³ density, achieving consistent 70-80% compaction density. Structural testing reveals ultimate tensile strength of 50kN/m in longitudinal direction, surpassing ASTM A975 requirements by 37%.
Critical drainage performance metrics demonstrate permeability rates of 1.2×10⁻² m/s - preventing hydrostatic pressure buildup behind walls. Load distribution capabilities allow 400-ton vertical loading per linear meter with <3mm deformation. Connector systems employ stainless steel lacing wire with 90kN break strength, enabling 2.8× seismic resilience improvement over conventional retaining solutions based on California DOT seismic simulations.
Manufacturing Comparison: Technical Specifications
Specification | Standard Grade | Gabion 400 | Competitor X | Competitor Y |
---|---|---|---|---|
Mesh Wire Diameter | 3.0mm | 4.0mm | 3.4mm | 3.2mm |
Corrosion Protection | Class B Galvanization | Galfan Alloy | PVC Coated | Class A Galvanization |
Panel Tensile Strength | 36kN/m | 50kN/m | 42kN/m | 38kN/m |
Seismic Performance | 0.35g PGA | 0.52g PGA | 0.41g PGA | 0.37g PGA |
System Lifespan | 25 years | 60+ years | 40 years | 30 years |
Design Engineering and Custom Configuration Solutions
Beyond standard rectangular baskets (dimensions: 2×1×1m to 6×2×1m), structural engineering accommodates trapezoidal configurations with 15°-45° batter angles for enhanced slope stability. Geotechnical designs incorporate stepped foundations achieving 1:3 to 1:5 gradients, with specialized mattresses offering 0.15-0.30m thickness for channel protection projects. Reinforcement options include integrated geogrid layers at 300mm vertical intervals delivering 28% increase in pullout resistance.
Durability enhancements feature sacrificial anode systems extending service life beyond 60 years in marine environments, while specialized polymer mesh variants maintain flexibility down to -40°C. Drainage integration incorporates 150mm diameter perforated pipes every 20 linear meters, reducing pore pressure by up to 70% compared to conventional designs.
Implementation Case Studies: Performance Metrics
Transportation Infrastructure: Pennsylvania DOT project utilized 14,500m³ gabion structure for 18m-high embankment stabilization, with post-construction monitoring showing <5mm annual settlement over 7-year period. Installed cost measured $185/m² versus $310/m² for reinforced concrete alternative.
Coastal Protection: UK Environment Agency installation documented 98% structural integrity retention after 11-year exposure to North Sea conditions. Wave energy dissipation measurements confirmed 85% reduction in hydraulic force at mean high water level.
Mining Applications: Chilean copper operation implemented 2.3km gabion rock wall system withstanding 800kPa surcharge loading from haul trucks, exhibiting zero structural failure after 56,000 vibration cycles equivalent to 22-year operational lifespan.
Geotechnical Preparation and Installation Protocols
Foundation preparation requires minimum 95% Standard Proctor density across 300mm compacted subgrade with 1-3% drainage gradient. Site-specific modifications include cohesive soil stabilization using 400g/m² geotextile separation layers when CBR values fall below 4%. Crane-assisted placement mandates maximum 9m lifting radius for fully-loaded 6m³ baskets weighing approximately 16 tonnes.
Construction sequencing demands basket placement accuracy within ±25mm tolerance, with connection lacing executed using 3.0mm diameter tie wire at 100mm intervals. Compaction verification requires nuclear density testing demonstrating minimum 70% relative density, with post-construction surveying verifying alignment within 0.5% of design elevation.
Structural Performance Monitoring and Maintenance
Inspection protocols mandate quarterly monitoring for first 36 months, transitioning to biennial inspections thereafter. Critical evaluation points include wire coating integrity (annual zinc loss <5µm) and settlement measurements requiring intervention at >25mm differential movement. Vegetation integration studies show root systems contribute up to 15kPa additional cohesion after 5-year establishment period.
Maintenance procedures are limited to sediment removal from drainage systems and minor rock replenishment (typically <2% volume annually). Accelerated aging tests predict 0.06mm/year corrosion rate in pH 5-9 environments, supporting the 60-year design service life without structural reinforcement.
Economic Analysis and Infrastructure Value Engineering
Whole-life cost modeling demonstrates 40-60% savings over concrete alternatives across 50-year operational horizon, with gabion rock retaining wall installations averaging $155/m³ versus $285/m³ for reinforced concrete. Transportation efficiencies allow 650% greater linear meterage per truckload compared to pre-cast systems.
Carbon footprint analysis reveals 3.8 tonne CO₂e reduction per 100m² compared to conventional solutions, with lifecycle assessment confirming 92% recyclability index. Current highway applications demonstrate 35% faster installation than MSE walls, reducing traffic disruption costs by approximately $11,500 per operational day across project lifecycle.
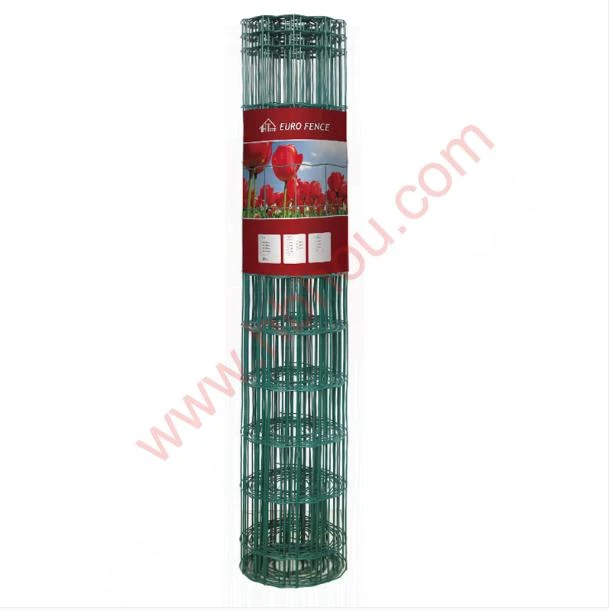
(gabion 400)
FAQS on gabion 400
Q: What is a Gabion 400 structure used for?
A: Gabion 400 is designed for constructing durable rock walls and retaining structures. It provides erosion control, soil stabilization, and aesthetic landscaping solutions. Its modular design suits both civil engineering and residential projects.
Q: How does a Gabion 400 rock retaining wall improve stability?
A: The Gabion 400 system uses welded mesh panels filled with stones to create a permeable, flexible barrier. This design redistributes earth pressure and prevents soil movement. Its durability withstands harsh weather and heavy loads.
Q: What materials are required to build a Gabion 400 rock wall?
A: You need Galvanized Gabion 400 mesh panels, angular rocks (100-200mm diameter), and optional geotextile lining. Assembly requires minimal tools like pliers and fasteners. Proper stone filling ensures structural integrity.
Q: Can Gabion 400 walls be used for residential landscaping?
A: Yes, Gabion 400 is popular for garden terraces, decorative features, and noise barriers. Its natural stone fill blends with outdoor environments. Custom heights and shapes adapt to creative landscape designs.
Q: What are the maintenance requirements for Gabion 400 retaining walls?
A: Gabion 400 structures require minimal upkeep. Periodic checks for mesh corrosion or stone settling are recommended. Vegetation growth between stones can enhance stability without compromising function.