Welding cast iron with stainless steel wire can be a complex process, but when done correctly, it can yield strong and durable joints. Cast iron is known for its excellent castability and wear resistance, making it a popular choice for various applications, including engine blocks and machinery parts. However, its brittleness poses challenges during welding, especially when using different materials like stainless steel.
To begin with, understanding the characteristics of both materials is crucial. Cast iron contains a high carbon content, which contributes to its hardness and brittleness. When exposed to high heat during welding, cast iron can develop cracks due to thermal stress. On the other hand, stainless steel, known for its corrosion resistance and ductility, requires different welding techniques and considerations. Combining the two materials necessitates careful attention to pre-heating, filler materials, and welding techniques.
Pre-heating the cast iron is a vital step in the welding process. By gradually heating the area to be welded to a temperature between 300°F to 500°F (150°C to 260°C), the risk of cracking can be significantly reduced. This pre-heat allows for a more controlled cooling process, minimizing the thermal shock that could lead to fractures.
When it comes to selecting the right filler material, stainless steel wire is an excellent choice due to its compatibility with various stainless steel grades. Stainless steel wires, such as ER309L, are recommended for welding cast iron because they can accommodate the differences in thermal expansion rates between cast iron and stainless steel. The use of stainless steel wire not only enhances the joint strength but also improves the overall corrosion resistance of the weld.
welding cast iron with stainless steel wire
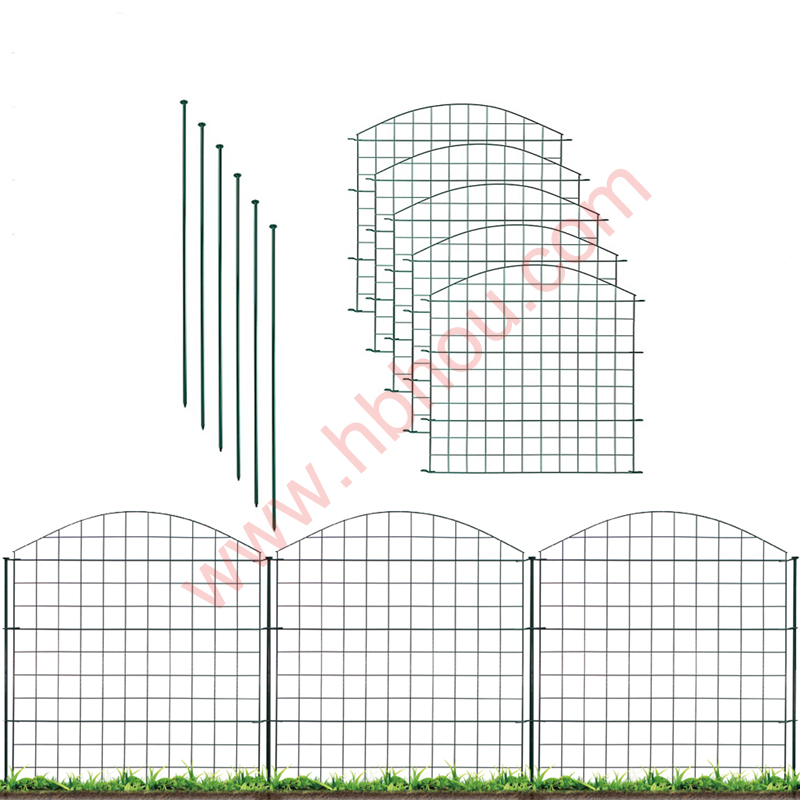
The welding technique employed is equally significant. A tig (Tungsten Inert Gas) welding approach is often favored because it provides better control over the arc and heat input. This precision is crucial for preventing overheating and ensuring that the weld pool remains manageable. Additionally, maintaining a consistent travel speed will help in achieving a uniform bead, further reducing the chances of defects.
After welding, it is essential to allow for a slow cooling period to alleviate any residual stresses in the joint. Post-weld heat treatment could also be beneficial, as it helps in relieving stresses and improving the mechanical properties of the weld.
In conclusion, welding cast iron with stainless steel wire is feasible and can yield durable results with proper techniques and precautions. By understanding the properties of the materials, implementing effective pre-heating strategies, selecting appropriate filler materials, and utilizing the right welding techniques, it is possible to achieve strong and lasting welded joints suitable for a variety of applications.