Welding Cast Iron with Flux Core Wire Techniques and Tips
Welding cast iron can be a challenging yet rewarding task, especially when using flux core wire. Cast iron presents unique properties, such as brittleness and a tendency to crack, making the welding process more complex than with other materials. Understanding the techniques and best practices for welding cast iron with flux core wire can help you achieve strong, lasting welds.
Understanding Cast Iron
Cast iron is an alloy containing iron, carbon, and silicon, with carbon levels typically between 2% and 4%. This composition gives cast iron its excellent castability and wear resistance but contributes to its brittleness. The high carbon content can lead to welding difficulties, such as cracking due to thermal stresses and the formation of hard, brittle microstructures.
Choosing the Right Flux Core Wire
When welding cast iron, the selection of flux core wire is critical. You should use a wire specifically designed for welding cast iron. Many professionals recommend using an E71T-1 or E71T-GS flux core wire due to its versatility and strong penetration. Ensure that the wire is compatible with the grades of cast iron you plan to weld.
Pre-Welding Preparation
Before you begin the welding process, proper surface preparation is essential. Clean the area to be welded thoroughly to remove any contaminants such as grease, oil, dirt, or rust. Utilizing a grinder or wire brush can help achieve a clean surface. Additionally, preheating the cast iron to a temperature of around 400°F (200°C) can reduce the risk of cracking, as it minimizes thermal stress.
Welding Techniques
welding cast iron with flux core wire
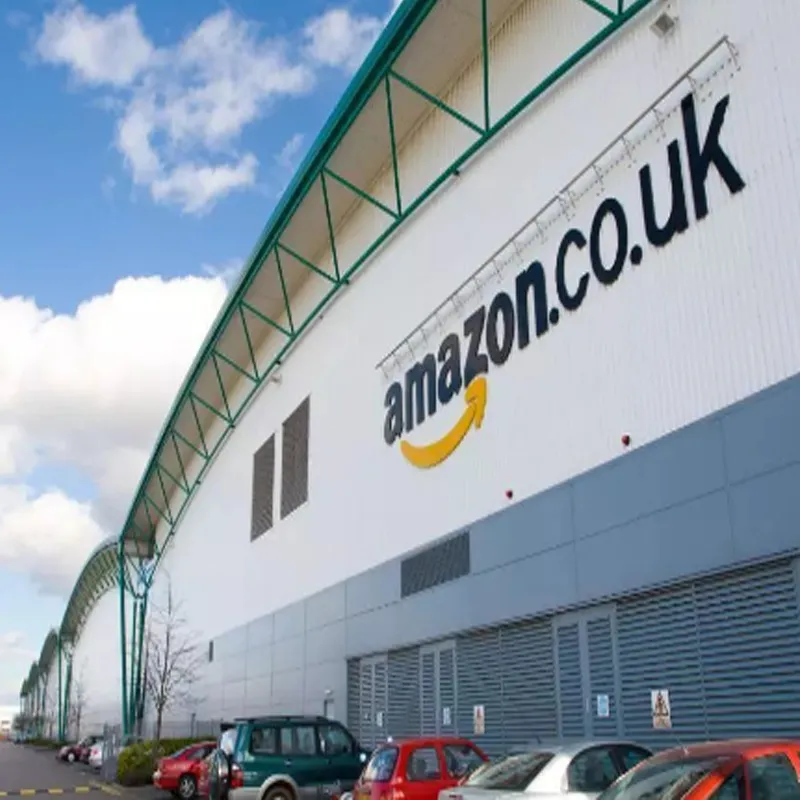
Once you’ve prepared your materials, it’s time to start welding. Here are some key techniques to keep in mind
.
1. Use Short Intervals Due to the brittleness of cast iron, apply heat in short intervals, using multiple passes if necessary. This method helps prevent overheating, which can lead to distortion and cracking.
2. Maintain a Steady Hand A steady hand is crucial in maintaining the quality of the weld. Try to create a consistent travel speed and keep the arc length short to ensure good penetration.
3. Build Up Thickness Gradually When welding thicker sections, build up the weld in layers rather than attempting to weld the entire thickness at once.
4. Peening After each weld pass, consider peening with a hammer to relieve residual stresses. This practice can help reduce the likelihood of cracking as the weld cools.
Post-Welding Considerations
After completing the weld, allow the joint to cool slowly. Rapid cooling can lead to thermal shock and cracks, compromising the integrity of the weld. Consider covering the welded area with an insulating blanket to control the cooling rate. Finally, inspect the weld for any defects, and if necessary, grind and polish to achieve a smooth finish.
Conclusion
Welding cast iron with flux core wire requires careful planning, the right materials, and precise techniques. By understanding the properties of cast iron and following the recommended practices, you can create strong, durable welds that stand the test of time. With persistence and skill, welding cast iron can be a successful venture that enhances your fabrication capabilities.