Welding Cast Iron with Stainless Steel Wire Techniques and Considerations
Welding cast iron presents unique challenges due to its brittleness and the presence of graphite structures that can affect the strength and integrity of the welded joint. However, with the appropriate techniques and materials, particularly the use of stainless steel welding wire, these challenges can be effectively managed. This article explores the principles, benefits, and methodologies associated with welding cast iron using stainless steel wire.
Understanding Cast Iron Properties
Cast iron is known for its excellent castability and wear resistance, making it a popular material in various applications such as machinery, engine blocks, and piping. Despite its advantageous properties, cast iron's high carbon content can lead to issues during welding, including cracking and poor fusion. The microstructure of cast iron, consisting of graphite flakes, complicates the welding process because these flakes can act as stress concentrators, resulting in weakened joints.
The Advantages of Stainless Steel Wire
Choosing to weld cast iron with stainless steel wire can provide several benefits. Stainless steel has a higher tensile strength and is less prone to corrosion compared to traditional cast iron. When welded, stainless steel can offer improved joint ductility and impact resistance, which is particularly important in high-stress applications. Furthermore, stainless steel provides a better aesthetic finish and corrosion resistance, which can enhance the durability of the repair or assembly.
Welding Techniques for Cast Iron
welding cast iron with stainless steel wire
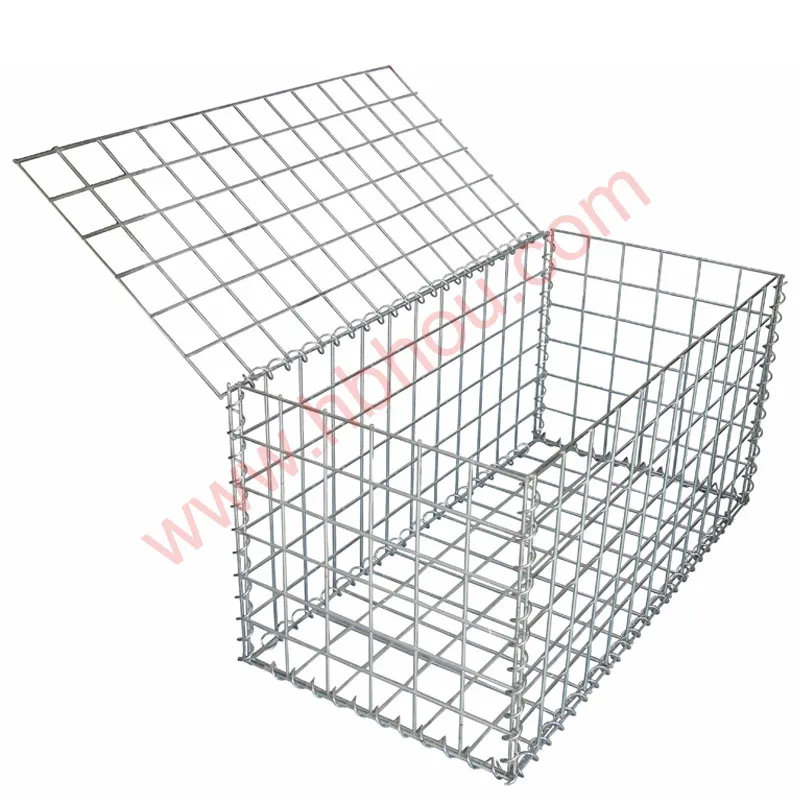
1. Preheating Before beginning the welding process, preheating the cast iron is critical. This step helps reduce the temperature gradient between the weld metal and the base material, minimizing the risk of cracking. Preheating to a temperature of around 300-600°F (150-315°C) is often recommended, although the exact temperature may vary based on the cast iron composition and section thickness.
2. Selection of Filler Material When selecting stainless steel wire for welding, it is crucial to choose an appropriate filler material that matches the properties of the cast iron being welded. Commonly used stainless steel filler materials include ER308L and ER316L wires, which are known for their good corrosion resistance and mechanical properties.
3. Welding Process The most suitable welding processes for cast iron with stainless steel wire include gas tungsten arc welding (TIG) and gas metal arc welding (GMAW). TIG welding is preferred for its precision, allowing for better control over the heat input and weld appearance. GMAW, with its faster deposition rates, can also be used effectively, particularly for larger repairs.
4. Post-Weld Treatment After welding, it is essential to perform post-weld heat treatment to relieve any residual stresses that may have developed during the cooling phase. This can involve reheating the welded joint and then allowing it to cool slowly in a controlled environment, further reducing the risk of cracking.
Conclusion
Welding cast iron with stainless steel wire is a viable solution that can enhance the performance and longevity of welded structures. By understanding the unique properties of cast iron, selecting appropriate filler materials, and employing effective welding techniques, welders can achieve strong and durable joints. As industrial applications continue to evolve, the combination of cast iron and stainless steel offers exciting possibilities for innovation in fabrication and repair, ensuring that cast iron remains a relevant material in modern engineering.