MIG Welding Cast Iron with Stainless Wire
MIG (Metal Inert Gas) welding is a popular welding method that offers versatility and ease of use, especially in various metals. When it comes to welding cast iron, which has its own unique set of challenges due to its brittleness and high carbon content, using stainless steel wire can be an effective method. This approach provides not only a strong bond but also enhances corrosion resistance, making it suitable for diverse applications.
Cast iron is widely used in construction, automotive components, and machinery due to its excellent castability and wear resistance. However, the inherent properties of cast iron, such as its brittleness, can lead to cracking during the welding process. To mitigate these risks, selecting the appropriate filler materials and using specific welding techniques is crucial.
When utilizing MIG welding for cast iron, one commonly considers using stainless steel wire as a filler. Stainless steel has better ductility and toughness than cast iron, which significantly reduces the likelihood of cracking. This method involves preparing the cast iron surface by thoroughly cleaning it to remove any grease, oils, or rust. Properly ground surfaces can enhance the quality of the weld.
The choice of stainless steel wire should be guided by the application. ER309L and ER308L are popular choices among welders for this purpose. ER309L is particularly effective for joining dissimilar metals, including stainless steel and cast iron. This wire contains a higher percentage of chromium and nickel, which allows for improved bonding and corrosion resistance. ER308L, while primarily used for stainless steel, can also be effective when welding cast iron with stainless filler due to its lower carbon content. This characteristic helps prevent excessive carbon migration from the cast iron into the weld, which can lead to brittleness.
mig welding cast iron with stainless wire
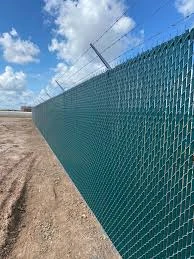
One of the key considerations when MIG welding cast iron with stainless wire is controlling the heat input. Excessive heat can cause the cast iron to warp or crack. It’s advisable to use a lower voltage and travel speed while ensuring proper gas coverage to protect the weld pool. Argon or a mix of argon and carbon dioxide is typically used as the shielding gas to protect the molten weld from atmospheric contamination.
Post-weld treatment is essential to alleviate residual stresses created during the welding process. Techniques such as slow cooling or stress relieving by heating the weld area can significantly improve the final mechanical properties of the welded joint.
Moreover, it is advisable to conduct a thorough inspection of the weld after it cools. Visual inspections, along with methods such as dye penetrant testing, can help identify any potential cracks or defects in the weld.
In summary, MIG welding cast iron with stainless wire is an effective technique that combines the durability of stainless steel with the practicality of cast iron. By selecting suitable filler materials, controlling the welding parameters, and implementing post-weld treatments, welders can produce high-quality joints that meet the requirements of various industries. This method not only enhances the durability but also extends the lifespan of cast iron components, making it a valuable technique in the manufacturing and repair sectors.