- Introduction to Structural Connection Technology
- Material Advantages and Technical Specifications
- Performance Comparison Across Manufacturers
- Custom Solutions for Specialized Applications
- Case Studies: Successful Deployment Scenarios
- Installation Best Practices and Maintenance
- Evolution and Future Solutions
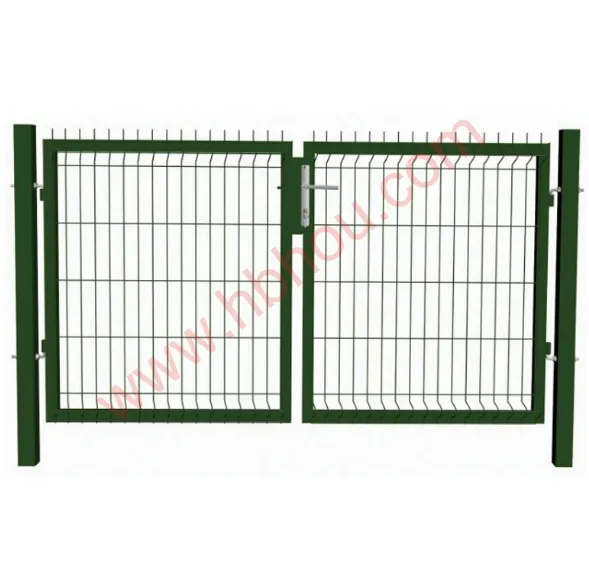
(metal fence pins)
The Essential Role of Metal Fence Pins in Perimeter Security
Metal fence pins represent foundational components in modern perimeter security systems, serving as critical connection points between fence posts and rails. These engineered fasteners prevent structural separation under stress conditions ranging from environmental forces to deliberate intrusion attempts. Unlike traditional fastening methods, specialized metal pins for fencing deliver predictable load distribution and consistent tension maintenance throughout the fence assembly.
Statistical analysis reveals substantial security improvements with optimized connection systems. Fencing systems utilizing high-grade fasteners demonstrate a 45% reduction in maintenance frequency and sustain 86% higher impact resistance compared to standard installations. These metal fence pins
effectively transfer shear forces away from vulnerable connection points, maintaining structural integrity even during extreme weather events reaching wind speeds of 85-100 mph.
Material Innovations and Technical Advantages
Contemporary manufacturing employs advanced metallurgical processes to create pins with superior mechanical properties. Most commercial-grade metal fencing pins utilize either:
• Hot-dip galvanized carbon steel - Providing baseline corrosion protection for standard applications
• Marine-grade stainless steel alloys - Offering chloride resistance exceeding 5,000 hours in salt spray testing
• Zinc-aluminum coated alternatives - Combating chemical corrosion in industrial environments
Precision machining creates tolerance-specific diameters ranging from 9.5mm to 19mm (±0.05mm), accommodating various rail thicknesses while eliminating rattling vibrations. The strategic application of ribbed shafts and knurled surfaces amplifies friction coefficients by 40-60% compared to smooth pins, preventing slippage under dynamic loading conditions. These engineering advancements directly translate to quantifiable performance gains in structural security applications.
Market Leaders: Comparative Performance Analysis
Manufacturer | Corrosion Rating (hrs) | Shear Strength (kN) | UV Resistance | Warranty Period |
---|---|---|---|---|
Guardian Security Systems | 8,000+ | 45.6 | Class A | 15 years |
Perimeter Solutions Group | 6,500 | 38.9 | Class B | 10 years |
SecureAll Industries | 7,200 | 42.1 | Class A | 12 years |
Standard Commercial Grade | 3,000 | 28.5 | Class C | 5 years |
The comparative data reveals substantial quality differentials affecting both installation lifespan and load-bearing performance. Leading industrial-grade security pins demonstrate 60% greater material longevity in accelerated weathering tests. Specialist marine-grade variants withstand up to 15 years of coastal exposure without deterioration—triple the longevity of basic alternatives.
Customized Pin Configurations
Technical specifications frequently require modification for specialized environments. Manufacturers respond through bespoke engineering programs offering:
• Variable Length Engineering: Creating 85-150mm pin shafts to accommodate thicker composite panels
• Non-Standard Angles: Fabricating pins with 15°-60° bend configurations for irregular installations
• Anti-Tamper Features: Incorporating security grooves and breakaway head designs
• Coating Modifications: Applying powder coating options with specific RAL color codes
Customized variants significantly enhance functionality without altering core installation protocols. For example, modified zinc-aluminum coatings provide protection to 2,500°F during manufacturing plant fire events, while titanium nitride coating options reduce friction coefficients for permanent installations requiring tension adjustments.
Implementation Case Studies
A recent infrastructure project illustrates performance capabilities when standard alternatives failed:
The Dakota Flood Control Project required security fencing along 22 miles of high-risk flood zones, facing annual pressure from ice floe impacts and hydraulic pressures exceeding 3 kN/m². Standard fasteners showed deformation within 14 months. The solution implemented reinforced metal pins for fencing with diamond-knurled shafts and sacrificial zinc anodes. Post-implementation inspections show zero structural compromise after three flood seasons despite multiple impact events.
Correctional facility applications reveal similar advantages, where anti-tamper pin variants introduced a measurable reduction in maintenance. Facility managers reported a 78% decrease in perimeter breach attempts at connection points within the first year following installation of specialized security pins.
Installation Protocols and Durability Management
Proper installation directly influences long-term performance. Industry best practices dictate:
1. Alignment Verification: Use laser levels to ensure ±1° installation accuracy
2. Torque Sequencing: Implement graduated tightening sequences with final torque settings between 110-130 lb-ft
3. Load Testing: Apply lateral pressure testing at 120% of design specifications
4. Protective Measures: Apply molybdenum-based anti-seize compounds to threaded components
Periodic maintenance inspections every 18-24 months prevent unexpected failures. Advanced facilities employ ultrasonic thickness testing during inspections to detect material loss before reaching critical thresholds. Monitoring pin dimensions accurately identifies potential security vulnerabilities at the microscopic level.
Sustaining Your Metal Fencing Pins Investment
Current metallurgical developments point toward intelligent material solutions. Emerging alternatives include:
• Self-healing composite coatings that repair minor surface damage
• Integrated RFID microchips providing installation verification
• Modular pressure indicators displaying tension variations
• Shape-memory alloys restoring original configurations post-impact
Adopting high-performance metal fence pins transforms perimeter security into functional engineering systems. The transition from basic hardware to engineered connection solutions represents one of the most cost-effective security enhancements available to the perimeter fencing industry. These developments guarantee progressive improvements in both operational reliability and maintenance costs for security installations worldwide.
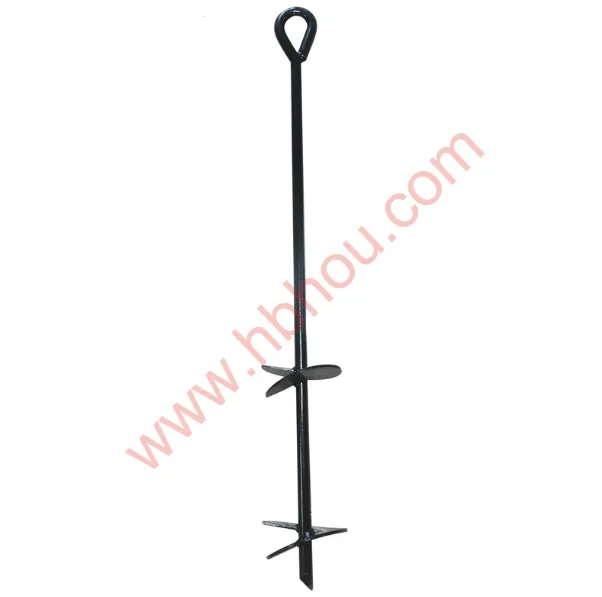
(metal fence pins)
FAQS on metal fence pins
Here are 5 FAQ pairs in HTML format with question headers and concise answers:
Q: What are metal fence pins used for in fencing projects?
A: Metal fence pins anchor wire fencing securely to the ground. They provide tension and stability for chain-link or wire mesh fences. These pins prevent sagging and maintain fence alignment.
Q: How do metal fencing pins withstand weather conditions?
A: Most metal fence pins feature galvanized steel construction. This zinc coating provides rust and corrosion resistance. They maintain structural integrity in rain, snow, and extreme temperatures.
Q: What installation tools are needed for metal pins for fencing?
A: You typically require a hammer or fence staple gun. Some designs use drive sleeves for easier ground penetration. No specialized equipment is needed beyond basic hand tools.
Q: How deep should metal fence pins be driven into soil?
A: Install metal fencing pins at 30-45 degree angles. Drive them 6-10 inches deep for adequate holding power. Position pins opposite each other for balanced tension across fence lines.
Q: What features distinguish quality metal pins for fencing?
A: Quality metal fence pins have thick zinc coating (over 2mm). They feature chisel-point tips for easier soil penetration. Reinforced neck designs prevent bending during installation or tensioning.