Understanding Iron Wire Size A Comprehensive Guide
Iron wire is a fundamental material used in various applications, ranging from construction to crafting. Its size and dimensions are critical factors that determine its strength, flexibility, and suitability for specific tasks. In this article, we will explore the different wire sizes of iron, how to choose the right one for your project, and the regulations and standards that govern wire sizing.
What is Iron Wire?
Iron wire is a durable and versatile material that has been used for centuries. Traditionally, iron wire was made through the process of drawing iron rods through a series of dies, reducing the diameter to the desired size. Today, advancements in metallurgy and manufacturing have led to the production of high-quality iron wires that come in various sizes and thicknesses.
Understanding Wire Size Measurements
When it comes to wire size, there are two primary measurement systems used the American Wire Gauge (AWG) system and the metric system.
1. American Wire Gauge (AWG) In the AWG system, wire sizes are expressed as a number, where a smaller number indicates a thicker wire. For example, a 10 AWG iron wire is thicker than a 20 AWG wire. The AWG system is commonly used in the United States for electrical wiring but can also be applicable to iron wires.
2. Metric System In the metric system, wire size is typically measured in millimeters (mm) and is more straightforward. A wire labeled as 1mm in diameter is simply one millimeter thick. This system is frequently used in countries that follow the International System of Units (SI).
Choosing the appropriate wire size for your project is essential, as it affects the wire's tensile strength, flexibility, and overall performance
.iron wire size
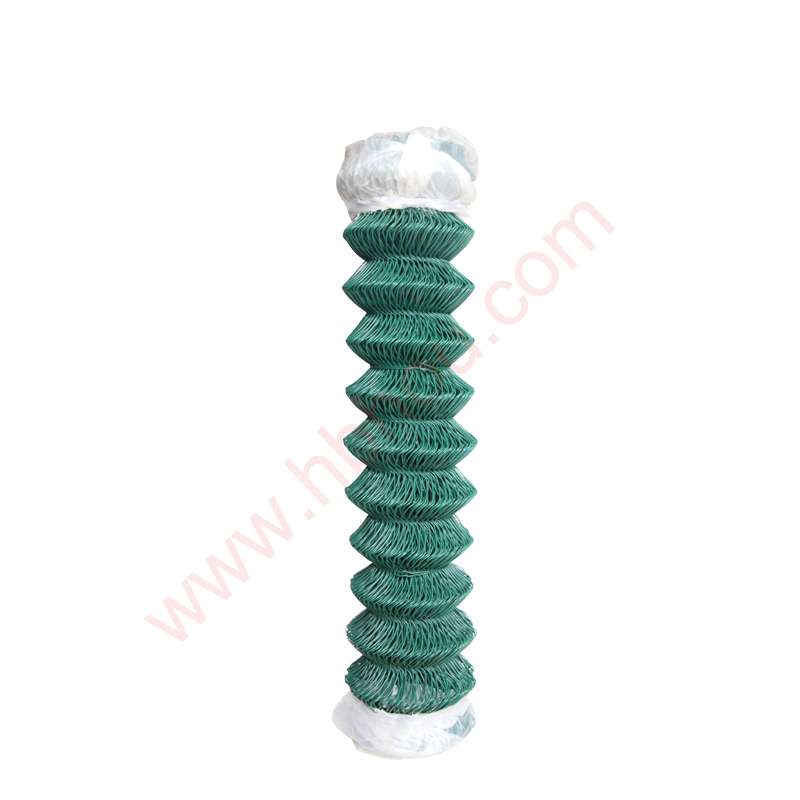
Factors to Consider When Choosing Iron Wire Size
1. Application The intended use of the iron wire significantly influences the size you should choose. For example, if you are using the wire for structural support in construction, a thicker wire would be necessary to bear heavy loads. On the other hand, for crafting or decorative purposes, a thinner wire may be suitable for flexibility and ease of handling.
2. Strength Requirements If the wire needs to support weight or withstand tension, selecting a thicker gauge is crucial. Consider the strength requirements of your project, as using an inadequate gauge may lead to failure.
3. Corrosion Resistance For applications that may expose the wire to moisture or corrosive environments, consider not only the size but also the type of iron wire. Some iron wires are coated or treated to resist rust and corrosion, which can extend their lifespan.
4. Flexibility vs. Rigidity Depending on whether you need a wire that can be easily shaped or one that remains rigid, you'll want to choose a size accordingly. Thinner wires tend to be more flexible, while thicker wires are usually more rigid.
Standards and Regulations
Different industries may have specific standards and regulations related to iron wire sizing. Adhesive bodies such as ASTM (American Society for Testing Materials) and ISO (International Organization for Standardization) provide guidelines that ensure safety and performance. When working on a project that requires compliance with regulations, always consult these standards to ensure you choose the correct wire size.
Conclusion
Selecting the appropriate iron wire size is vital to the success of your project—whether it’s for construction, crafting, or any other application. Understanding the measurement systems, the factors that influence wire size decisions, and the relevant standards will help you make informed choices. Always consider the specific needs of your project and consult professional guidelines if necessary. By doing so, you can ensure that your selection will provide the durability, strength, and flexibility required for optimal performance.