The Role of Stainless Steel Plant Supports in Industrial Applications
Stainless steel is renowned for its strength, durability, and resistance to corrosion, making it an ideal material for a variety of industrial applications. One of the critical components in the infrastructure of industrial plants is the support systems, which provide stability and functionality for piping, equipment, and structures. This article delves into the significance of stainless steel plant supports, their advantages, and the various applications in different industries.
Importance of Plant Supports
Plant supports are essential in ensuring the safe and efficient operation of industrial facilities. They are designed to hold and secure pipes, ducts, and other structural elements, preventing them from sagging or failing under pressure. In industries such as oil and gas, chemical processing, and manufacturing, the integrity of the support system directly affects operational safety and efficiency. Any failure in these systems can lead to costly downtime, hazardous leaks, and potential accidents.
Advantages of Stainless Steel
The choice of stainless steel for plant supports offers several advantages
1. Corrosion Resistance One of the most significant benefits of stainless steel is its exceptional resistance to corrosion. This characteristic is particularly important in environments that expose supports to harsh chemicals, moisture, and extreme temperatures. Stainless steel maintains its structural integrity over time, reducing the need for frequent replacements and maintenance.
2. Strength and Durability Stainless steel provides excellent strength-to-weight ratios, enabling it to support heavy loads without compromising stability. Its durability ensures that supports can withstand mechanical stresses, vibrations, and thermal expansions that are common in industrial settings.
3. Aesthetic Appeal Aside from functional benefits, stainless steel offers a sleek and modern appearance. This aesthetic quality makes it suitable for applications where visual appeal is important, such as in food manufacturing or pharmaceutical facilities.
stainless steel plant supports
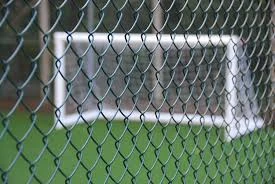
4. Ease of Maintenance Stainless steel is easy to clean and maintain, which is crucial in industries where hygiene is a priority. Its smooth surface minimizes the accumulation of dirt and bacteria, ensuring compliance with health and safety standards.
Applications of Stainless Steel Supports
Stainless steel plant supports are employed across various industries, demonstrating their versatility
- Chemical Processing In chemical plants, stainless steel supports are used to secure pipelines carrying corrosive substances. This ensures the safety of the operation by preventing leaks and spills that could lead to environmental hazards.
- Oil and Gas The oil and gas industry relies heavily on robust support systems for drilling rigs and refineries. Stainless steel's resistance to pitting and crevice corrosion, especially in saltwater environments, makes it an ideal choice for offshore applications.
- Food and Beverage In food processing facilities, maintaining hygiene is paramount. Stainless steel supports help construct sanitary piping systems, ensuring that the food supply remains uncontaminated.
- Pharmaceuticals The pharmaceutical industry requires stringent control over cleanliness and contamination. Stainless steel supports help achieve this by providing a material that can withstand rigorous cleaning processes while maintaining structural performance.
Conclusion
Stainless steel plant supports play a crucial role in the stability and safety of various industrial systems. Their unique properties—such as corrosion resistance, strength, and ease of maintenance—make them an invaluable asset across multiple sectors. As industries continue to evolve and face new challenges, the adoption of high-quality, durable materials like stainless steel will remain a critical factor in enhancing operational efficiency and safety. By investing in stainless steel supports, industries can ensure a reliable infrastructure capable of meeting the demands of modern manufacturing and processing environments.