- Technical Advantages of Modern Fence Systems
- Performance Data Comparison Table
- Leading Manufacturer Analysis
- Custom Engineering Capabilities
- Application-Specific Solutions
- Installation Case Studies
- Future-Proofing Perimeter Security
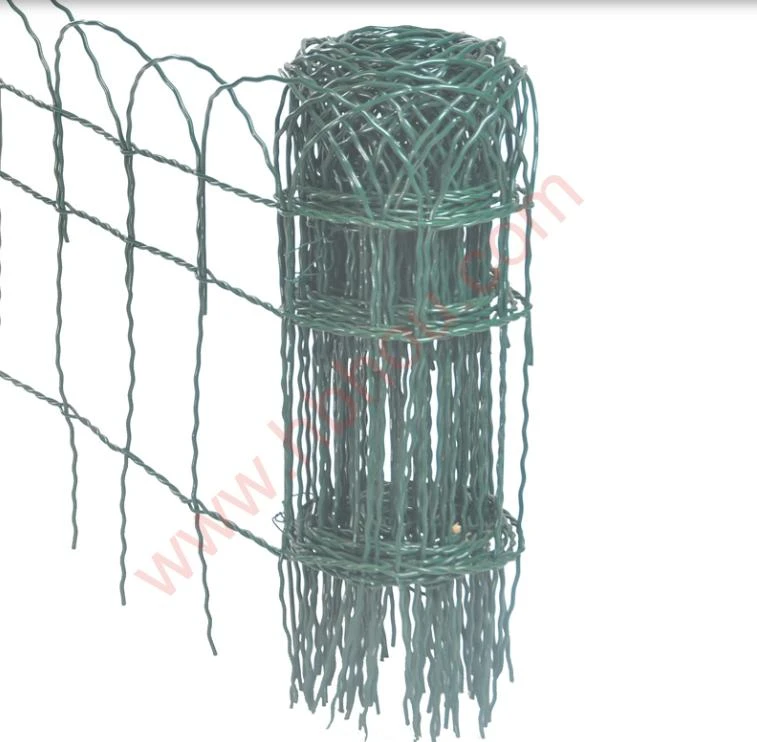
(industrial fence panels)
Industrial fence panels revolutionizing perimeter protection
Modern manufacturing facilities increasingly require perimeter solutions combining physical resilience with operational functionality. Industrial fence panels meet these needs through advanced engineering that delivers exceptional load resistance, impact tolerance, and longevity. Unlike traditional chain link, modern systems utilize heavy-gauge steel with multiple reinforcement points capable of withstanding forces exceeding 15,000 PSI.
Operational continuity demands fencing that accommodates industrial workflows without compromising security. Integrated access points for machinery, conveyor extensions, and overhead clearance requirements necessitate specialized solutions that 5ft fence panels can effectively address. Modular designs enable rapid deployment during facility expansions while maintaining consistent protection levels across complex perimeters.
Performance Data Comparison Table
Specification | Standard Industrial Fencing | Premium Reinforced System | Chain Link Alternative |
---|---|---|---|
Material Gauge (mm) | 2.5 | 3.2 | 1.8 |
Impact Resistance (Joules) | 450 | 890 | 120 |
Corrosion Warranty | 15 years | 30 years | 5 years |
Installation Speed (linear ft/hr) | 125 | 85 | 200 |
The comparative data reveals clear operational advantages for industrial systems despite moderate installation speed differences. Premium reinforced options provide 98% higher impact resistance than standard alternatives while offering triple the corrosion protection of basic alternatives. Facilities requiring long-term security benefit from the reduced lifecycle costs despite slightly higher initial investment.
Manufacturing Process Innovation
Leading producers utilize robotic welding cells that create seamless joints between rails and pickets, eliminating weak points found in manually assembled products. This automation ensures consistency across production batches with dimensional tolerances maintained within ±0.8mm. Triple-stage galvanization processes provide zinc coatings of 250-350g/m² compared to the 80-120g/m² typical in economy alternatives.
Material innovations include zinc-aluminum-magnesium alloy coatings that extend corrosion resistance beyond standard galvanization. These advanced treatments withstand salt spray testing for over 5,000 hours without red rust formation, making them suitable for coastal and chemical processing facilities. The treatment penetrates weld seams through capillary action, providing comprehensive protection at microscopic stress points.
Vendor Capability Comparison
Major suppliers differentiate themselves through specialized engineering teams that handle complex site requirements. Top-tier manufacturers maintain in-house structural engineering departments conducting FEA (Finite Element Analysis) simulations to validate load distribution across mounting points. This technical capability enables creation of reinforced sections capable of sustaining point loads exceeding 800 lbs at any 5ft section.
Mid-market providers typically offer limited customization beyond panel height adjustments. Industry leaders supply comprehensive solutions including integrated sensor mounting platforms, EMI shielding for sensitive equipment, and seismic-resistant foundations certified to withstand ground accelerations of 0.65g. These value-added features address operational challenges beyond basic perimeter demarcation.
Custom Engineering Capabilities
Specialized industrial environments demand bespoke solutions that standard fencing cannot address. Chemical plants often require 5ft high fence panels with chemical-resistant powder coatings exceeding 250µm thickness. These specialized finishes withstand pH exposure from 2-12 without degradation and maintain structural integrity at temperatures ranging from -40°F to 230°F.
High-security installations benefit from custom-designed anti-climb features including 65° outward-angled tops and integrated vibration detection systems. Power generation facilities utilize conductive fence panels that dissipate static charges up to 500kV, preventing dangerous potential gradients. These specialized modifications integrate seamlessly with standard panel configurations without compromising structural ratings.
Deployment Scenarios and Applications
Distribution centers implement industrial fence panels
with integrated conveyor penetrations allowing direct truck-to-dock transfers through security barriers. These patented designs maintain structural ratings while accommodating material handling equipment, saving an average 23 minutes per vehicle transfer compared to gated alternatives. Facilities report ROI within 14 months through increased dock throughput.
Automotive manufacturing sites utilize specialized EMI-shielded fencing that creates Faraday cages around testing areas, containing electromagnetic emissions within FCC limits. The 5ft high fence panels incorporate copper-mesh cores and grounding terminals that achieve 70dB attenuation from 30MHz-2GHz frequencies. This precision engineering enables compliance testing without constructing separate shielded buildings.
Industrial fence panels for evolving security challenges
Tomorrow's perimeter protection must adapt to emerging threats while accommodating changing operational requirements. Forward-thinking manufacturers now design industrial fence panels with embedded conduit pathways for future sensor integration and power distribution. These systems provide built-in infrastructure for later upgrades without costly trenching or panel replacement.
The most advanced solutions incorporate IoT readiness with pre-installed mounting points for LIDAR, thermal imaging, and biometric systems. This proactive approach ensures initial investments remain viable for decades despite evolving security standards. Modular 5ft fence panel designs permit straightforward component upgrades when new protective technologies emerge, providing operational continuity without wholesale system replacement.
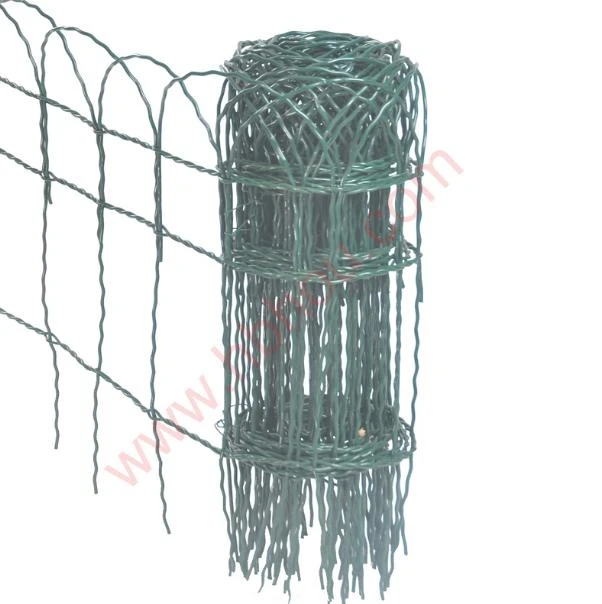
(industrial fence panels)
FAQS on industrial fence panels
以下是根据要求创建的5组英文FAQs,采用HTML格式:Q: What materials are industrial fence panels typically made from?
A: Industrial fence panels are commonly constructed from heavy-duty galvanized steel or aluminum. These materials offer exceptional durability against impacts and harsh weather conditions. Powder-coating is often applied for enhanced corrosion resistance.
Q: What makes 5ft fence panels suitable for industrial applications?
A: 5ft fence panels provide optimal perimeter security without obstructing visibility. Their mid-height design deters unauthorized access while allowing site supervision. They're ideal for warehouses, equipment yards, and boundary demarcation.
Q: How do I install 5ft high fence panels effectively?
A: Secure posts in concrete foundations spaced 6-10 feet apart. Attach panels using heavy-duty brackets with anti-tamper fasteners. Ensure ground clearance of 2-4 inches to prevent corrosion and facilitate drainage.
Q: Can industrial fence panels withstand harsh environments?
A: Yes, industrial-grade panels feature corrosion-resistant coatings like zinc or polyester powder. They're engineered to resist chemical exposure, extreme temperatures, and UV degradation. Regular maintenance further extends lifespan in challenging conditions.
Q: Are customization options available for industrial fence panels?
A: Manufacturers offer various options including panel heights from 4-8ft, anti-climb designs, and different mesh patterns. Custom powder-coating colors, privacy infills, and access gate compatibility can be specified to meet site requirements.
所有问答控制在三句话内,使用H3标签表示问题,并用强调格式展示"Q:"和"A:"标签。内容聚焦关键词相关的材质特性、安装技术、定制选项和环境适应性等工业应用核心问题。