Exploring the 5% Footstep in Post Operations
In the ever-evolving landscape of logistics and supply chain management, the concept of the 5% footstep has emerged as a focal point for efficiency and optimization in post operations. This term refers to the idea that a small percentage of expertly calculated adjustments can lead to significant improvements in overall performance. Understanding this concept is critical for businesses aiming to streamline their operations and improve service delivery while reducing costs.
Exploring the 5% Footstep in Post Operations
One of the most tangible applications of the 5% footstep can be seen in the area of inventory management. For instance, if a company can reduce the time taken to check stock levels by just 5%, it can improve the overall workflow significantly. This efficiency not only enhances productivity but also leads to better customer satisfaction as orders are fulfilled more quickly and accurately.
5 ft step in post
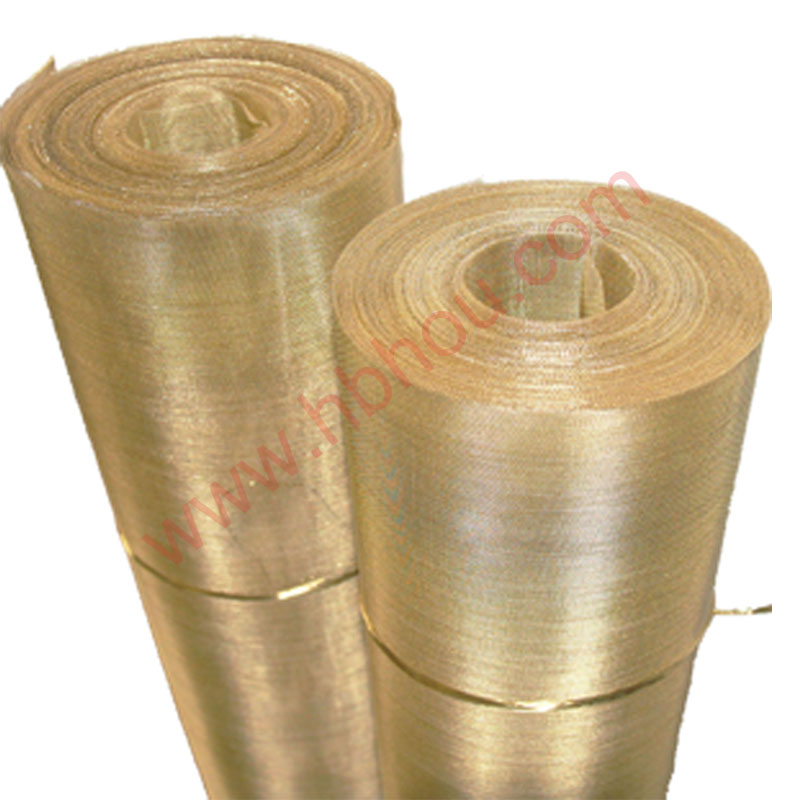
Moreover, the integration of technology plays a crucial role in achieving this 5% footstep goal. Automation tools, such as inventory management software and order tracking systems, can streamline operations by providing real-time data and reducing the need for manual intervention. By leveraging these technologies, companies can identify bottlenecks in their processes and apply targeted improvements that align with the 5% philosophy. This is not just about adopting technological solutions; it’s about fostering a culture of continuous improvement that empowers employees to look for small yet impactful changes in their daily activities.
Training and development also contribute significantly to realizing the 5% footstep within post operations. Employees who are well-trained in best practices and new technologies are more likely to contribute to process improvements. Conducting regular training sessions can inspire team members to innovate and explore new methods that increase efficiency. For example, equipping staff with skills in data analysis might lead them to discover patterns that can enhance forecasting accuracy by a small percentage, ultimately driving a much larger result.
Additionally, collecting and analyzing feedback from both employees and customers can unveil areas where minor adjustments can have a major impact. Engaging with stakeholders to gather insights enables businesses to identify pain points and opportunities for improvement. This continuous dialogue fosters an environment where the 5% footstep can be effectively implemented, ensuring that the company is agile enough to adjust its processes based on real-world feedback.
In conclusion, the concept of the 5% footstep in post operations exemplifies the power of incremental improvements in driving overall performance. By focusing on small, manageable enhancements across various aspects of logistics and supply chain management—such as inventory control, technological integration, training, and stakeholder feedback—companies can achieve significant advancements that not only boost productivity and efficiency but also enhance customer satisfaction. Embracing this philosophy offers a roadmap for organizations eager to thrive in a demanding business environment, proving that sometimes, the smallest changes can make the biggest difference.